As part of the Titan IV missile system program at Cape Canaveral, the
U.S. Air Force in 1988 undertook the construction of a Solid Motor Assembly
Building (SMAB). The design services for this project were provided by
Bechtel of San Francisco, and the Mobile District of the U. S. Army Corps of
Engineers acted as Construction Manager. With a "footprint" larger than a
football field, and over 225 feet tall, the SMAB interior is completely open
to allow movement of the rocket assembly. Two huge overhead cranes, of 500
ton and 220 ton capacity, provide mobility of the work components. At the
southern end of the building is a propellant assembly area called the
"stacking cells".
The project was set for bids in November 1989, with an original cost
estimated by the USAF/COE ranging from $62,578,969 to $89,000,000. Bids were
received, and the pricing was finalized in January 1990, with the best and
final offer made by Centex-Rooney, Inc. at a price of $39,976,984.
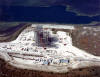 Construction work began in May of 1990 with an established contract
completion date of October 15, 1991. The Contract for this project contained
a clause establishing the withholding of liquidated damages in the event of
late completion by the Contractor.
The project was constructed from south to north by dividing the building
into four quadrants, with each quadrant having ten erection "sequences". The
construction sequence of this building was unique because the miscellaneous
metals (steel and aluminum checkered plate, handrail and stairs) was to be
installed simultaneously with the structural steel frame. Normally, concrete
placement operations and/or other activities create a gap between the
erection of the structural steel and the installation of the miscellaneous
metals.
In addition to the Air Force, Corps of Engineers, Bechtel, and
Centex-Rooney, other key players in the dispute which arose on this project
were Montague-Betts Company, Inc., Rooney's steel subcontractor, and
Copeland Steel Erectors, Montague-Betts' Steel Erection Sub-subcontractor.
During the course of construction, the project experienced late and
out-of-sequence delivery of Miscellaneous Metals, as well as the delivery of
incorrectly fabricated Miscellaneous Metals. Copeland Steel Erectors, Inc.
incurred the brunt of the damages resulting therefrom, and requested that
BRITTON review the project and assist by quantifying the additional and
extra costs arising from the late, out-of-sequence, and mis-fabricated
Miscellaneous Metals.
BRITTON's investigation incorporated "Measured Mile" Productivity Assessment
Techniques, and concluded that Copeland incurred at least $507,464.69 in
unforeseeable additional costs. The areas of damage were: Overtime Premium
Costs, Lost Productivity on Structural and Miscellaneous Erection, Added
Tool Costs, Added Equipment Costs, Additional Supervision and Quality
Control Personnel, Additional Costs for Corrective Work resulting from
Fabrication Errors, and Crane Overtime.
Through contemporaneous negotiation with Montague-Betts, Copeland was able
to recover the majority of its losses before the project completed. The
remaining Copeland losses were recovered at a later date, as part of a
mediated settlement of a $3.5 million+ Montague-Betts claim against the
Owner. |